I went to Stitches West at the Santa Clara Convention Center this morning to do a spinning demo, and of course since I was then in for free, some shopping.
It’s kinda like MacWorld for yarn. It would be dangerous if I bought knitting yarn, but typically I don’t. There were more vendors with spinning equipment and fiber, which was nice. I of course bought stuff I didn’t intend to. I wasn’t organizing this demo but only showing up to spin for a couple hours. I did teach so I wasn’t a complete slug. But I might have been more focused if I had actually had breakfast. Or lunch.
The demo was not the usual guild thing but for the Spinning and Weaving Association, a trade group of manufacturers and retailers. We were teaching, but not with the box of CD spindles the guild has. I got to play with a Ladybug wheel from Schacht, a beginner wheel less expensive than the Matchless.
It’s a nice little wheel, but I have to say I’m still a Lendrum partisan. The way it was set up was too slow for the kind of yarn I spin and too fast for real beginners. From looking on the website I think it had the medium whorl rather than the slow one but I’m not really sure. I found the scotch tension adjustment a little fussy, with the small plastic knob slipping when I tried to adjust it. Apparently it can also be set up for double drive, which I wouldn’t recommend for a first wheel. (Yes, when it works it’s wonderful. But getting it set Just Right is a bother.)
We had several small rigid heddle looms designed to use typical knitting yarns. They were already warped, I didn’t play with them but they seemed to be typical for the style. They had floor stands, which was nice. I really don’t know the manufacturer, I thought they might be the Knitter’s Loom, but it seems that Ashford is not a member of the association.
There was a small drum carder also, I carded some random layered batts and was spinning huge fluffy woolen yarn. Entirely unlike what I normally do, but suited to the fiber and equipment. Everybody seemed to like it and it got people’s attention.
I then spent about 90 minutes doing a fast tour of the show. I got a new spindle, some hand-dyed silk fiber and a length of Japanese silk fabric. Here’s a summary of the haul:
Hand-painted tussah silk from Fiber Fiend. It’s in blue, gray and purple in a colorway called Blackberry Swirl. Also a Maggie spindle from Carolina Homespun (27g I think the label said, before I lost it.)
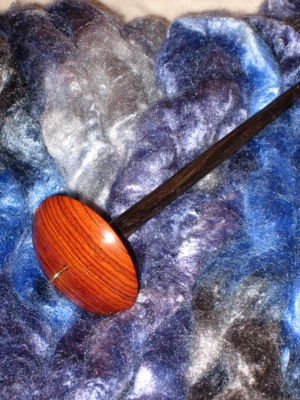
The silk from Japan with a floral design was from John Marshall. No way I can afford any of his own work, but this was a nice piece he found in Japan. He told me how they are turning up now because people aren’t doing much traditional work anymore and you can find them discontinued. Good for shoppers, at least the Americans who are buying wholesale and bringing them back, but bad for the craft. I’m not sure of the exact technique but boy is it nice. It has a large group of flowers on branches on each end and some additional flowers between. I’m guessing it was originally intended for kimono, with the large design.
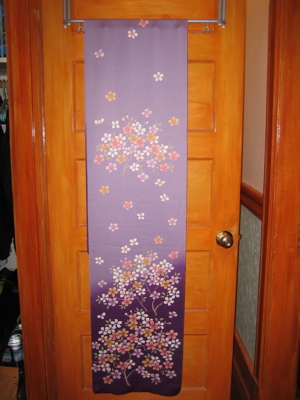